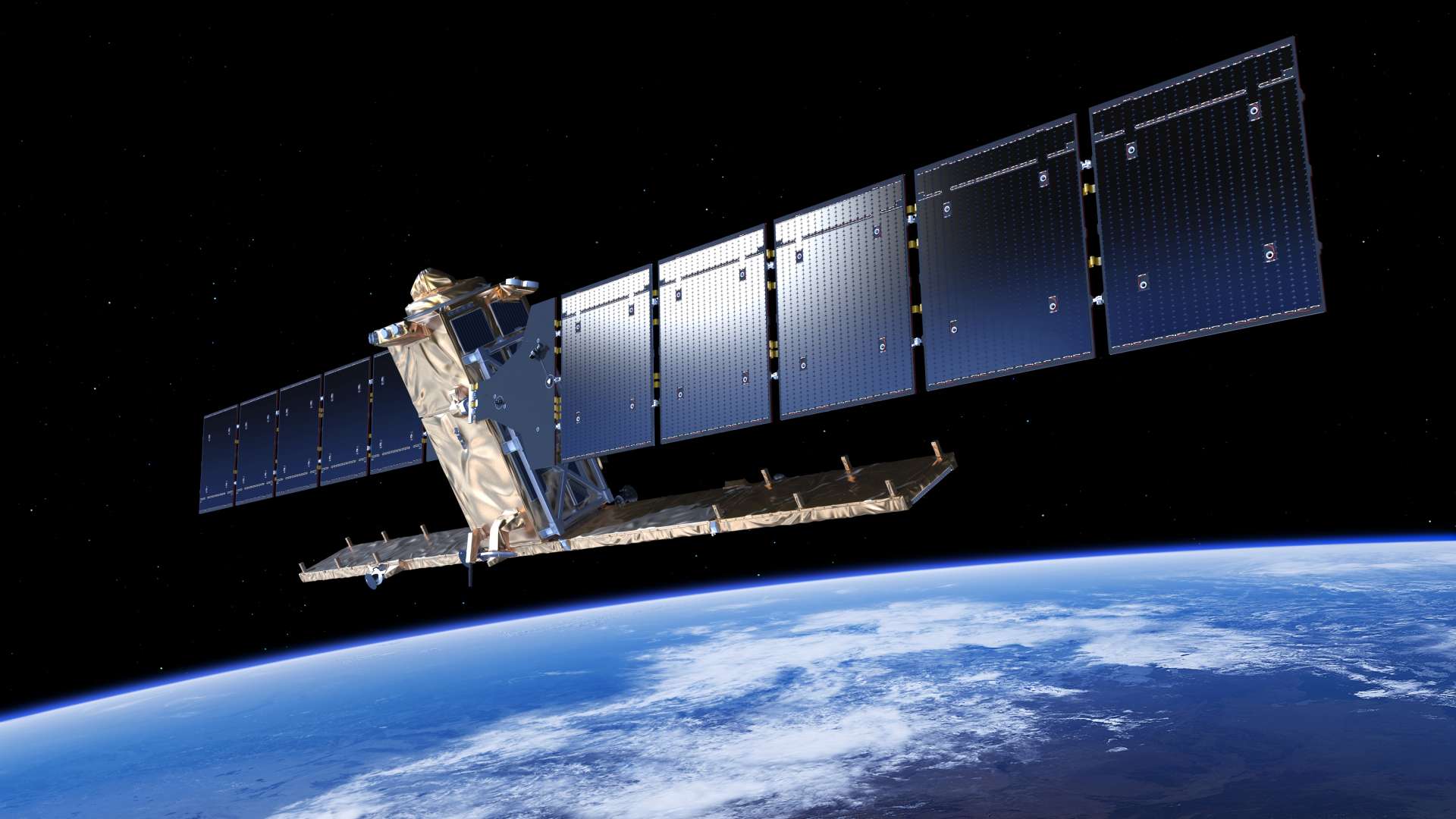
ATG Innovation completes design, analysis and manufacture of a fully representative lattice satellite central tube
ATG Innovation Ltd., the Irish subsidiary of ATG Europe, recently completed a milestone project in the continued development of ATG’s patented composite lattice technology, building on the extensive work undertaken on this topic by ATG to date. The project focused on assessing interface zones within the composite lattice structures developed by ATG, as these form the integration points for traditional flight hardware surrounding the spacecraft structure. This included the design, analysis, manufacture, and testing of element level interface specimens, before proceeding to the manufacturing and testing of a full-scale representative satellite central tube (SCT) demonstrator using the requirements from the service module of the European Space Agency’s PLATO satellite. This project was conducted under an ESA Science Directorate Core Technology Program (CTP) with the backing of Enterprise Ireland.
Multiple attachment design concepts were integrated into the lattice design to accommodate the various interface requirements of a satellite central tube. These concepts included various laminate patch configurations directly integrated into the lattice structure during layup, thus maintaining optimal structural integrity of the component. In addition, a one-piece aluminum ring was designed to provide an efficient hybrid joint with the lattice cylinder, while also meeting the interface requirements of a standard PAS 1666 adaptor, thus facilitating the interface with the launch vehicle. The mass of the full-scale lattice satellite central tube including the aluminum interface ring is 36.73kg, which is a 37% mass-saving over the current monolithic composite design scheduled to fly on PLATO in 2026.
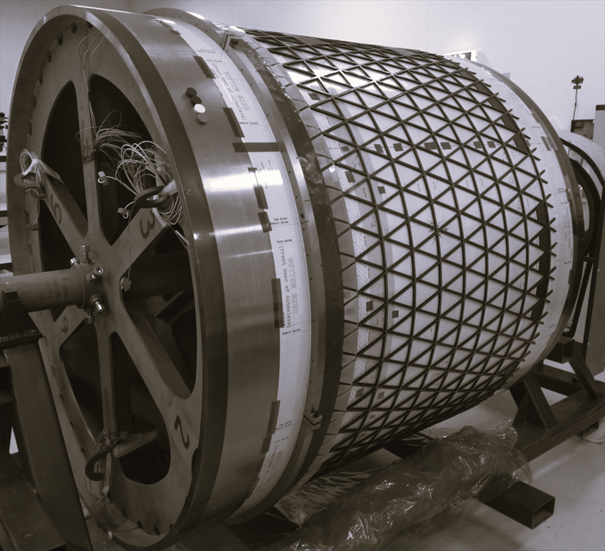
Lattice structure layup phase
Lattice cylinder manufacturing followed the patented methods developed by ATG, with all activities undertaken at our manufacturing partner ÉireComposites’ facilities, including full-time support from ATG. The laminate patches used for providing attachment points in the structure, are directly integrated into the layup. One of the main benefits of the design and manufacturing methodology employed by ATG is the ability to tailor patch locations and thicknesses right up to the start of the layup, giving added flexibility for changes as a design or product progresses. The entire part was cured in an autoclave in a one-shot process and achieved conformance to all design tolerances.
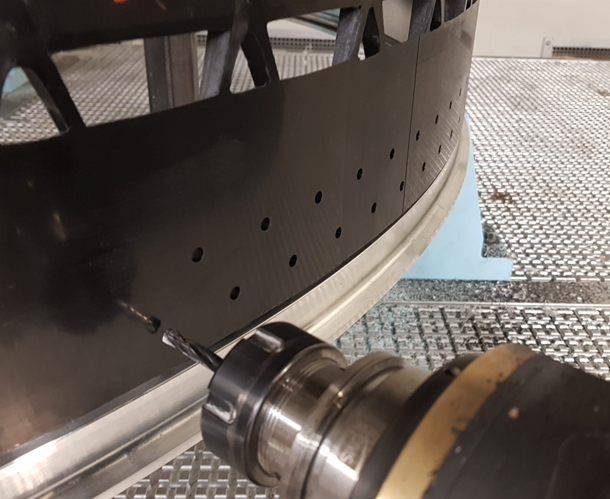
Drilling of holes for fastener installation in the hybrid joint between the composite lattice cylinder and aluminium interface ring
Once the composite lattice cylinder was formed, the aluminium interface ring was bonded to the monolithic laminate region of the structure followed by drilling of holes in the ring and patches using an automated CNC machine. Once completed, all inserts and fasteners were installed where necessary.
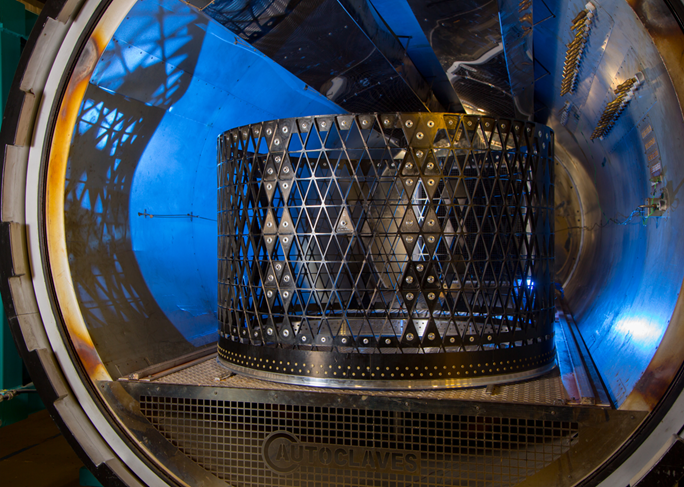
ATG’s assembled composite lattice satellite central tube
The culmination of years of work, this could not have been accomplished without the dedication of the composites team here at ATG, along with the time and support of all our project partners including ÉireComposites and Enterprise Ireland. The quality of the final product is a testament to the attention to detail that the entire team has placed in this work and is another step for ATG on our quest to accelerate the light-weighting of future spacecraft structures.
For more information please contact:
ATG Communication
Space Business Park
Huygensstraat 34
2201 DK Noordwijk (NL)communication@atg-europe.com
T: +31 (0)71 579 5500